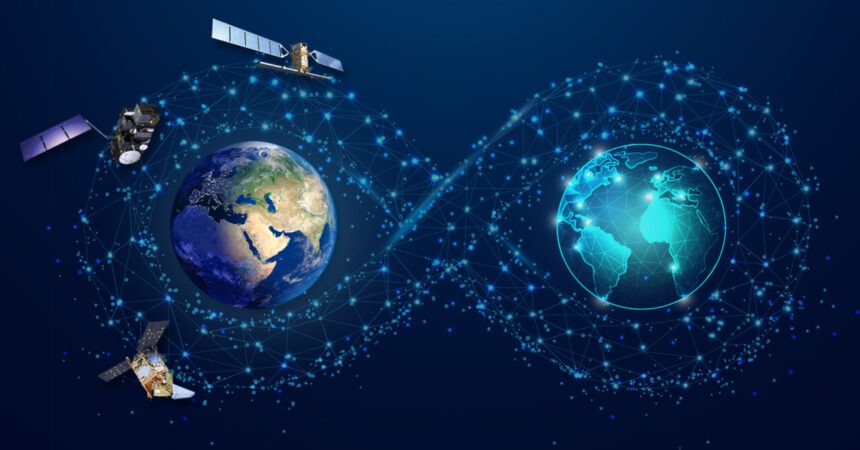
Digital Platforms for the "Factory of the Future" in the Space Industry
One of the three main pillars of Astra is its second work package, dedicated to digital platforms serving the aerospace industry. While the first work package primarily emphasizes hardware technology development, the second pillar of Astra centers on the software industry.
The ultimate goal is to create digital platforms that drive innovation in research and optimize supply chains already active in the space sector, such as Thales Alenia, one of Astra’s two private partners.
Digitalizing production is key to what has been called the "Factory of the Future" within the framework of the Fourth Industrial Revolution, commonly known as Industry 4.0. At its core, this paradigm focuses on industrial automation. The virtual and digital replication of industrial processes—from early engineering stages to full-scale production—has the potential to revolutionize cost efficiency, productivity, and effectiveness. One of the first sectors where these methods have been implemented is the automotive sector.
A key focus of Astra’s researchers is the implementation of digital twins, a concept gaining traction across industries. A digital twin is not merely a digital model but a virtual representation of an object or system that evolves alongside the physical entity throughout its lifecycle. It is updated in real time through simulation and learning mechanisms, often augmented by artificial intelligence, which will be explored in the next articles.
Production equipment is integrated into a centralized system for data storage and management. Real-time data processing enables the monitoring of production processes in alignment with the digital twin framework. This virtualization and modeling of processes enable optimal production planning. Such advancements are being applied to a case study involving the Crystal Eye, a flagship product in Astra’s roadmap, that we’ve explored in previous articles.
Challenges of Implementing Digital Twins for Space Applications
Developing reliable digital simulation systems for space applications is a formidable challenge. Space technologies demand extraordinary reliability, as they must operate in physical conditions vastly different from those on Earth. This discrepancy necessitates robust simulation systems capable of handling these unique environmental constraints.
Astra is committed to meeting these stringent quality standards. "We are working on scheduling tasks for a satellite developed by Thales Alenia," explains Patrizio Pelliccione, Full Professor at the Gran Sasso Science Institute (GSSI), where he leads the Computer Science area and oversees Astra's second work package.
"What we are attempting to do with our project partners," Pelliccione continues, "is to define a mechanism for optimizing the operation and exploitation of a satellite already in orbit. We are achieving this through the digital twin paradigm."
This approach encompasses multiple dimensions, ranging from the satellite's physical operations — such as rotation, observation and avionics — to its role in scientific research and service delivery.
Simulation and Prototyping Through Digital Twins
Practically, this involves creating a software representation in a highly sophisticated simulator. Astra's research team uses this simulator to validate the organization of tasks and temporal functionality of the satellite. "Through digital twins, we can assess computational usage, determine if adjustments are needed, and even add or remove functionalities," emphasizes the GSSI professor.
This process fosters the generation of knowledge, the creation of customized research prototypes, and the simulation of potential problem-solving scenarios for in-orbit challenges. It represents pure research experimentation conducted on Earth, always with an eye toward the skies.
Photo: ESA